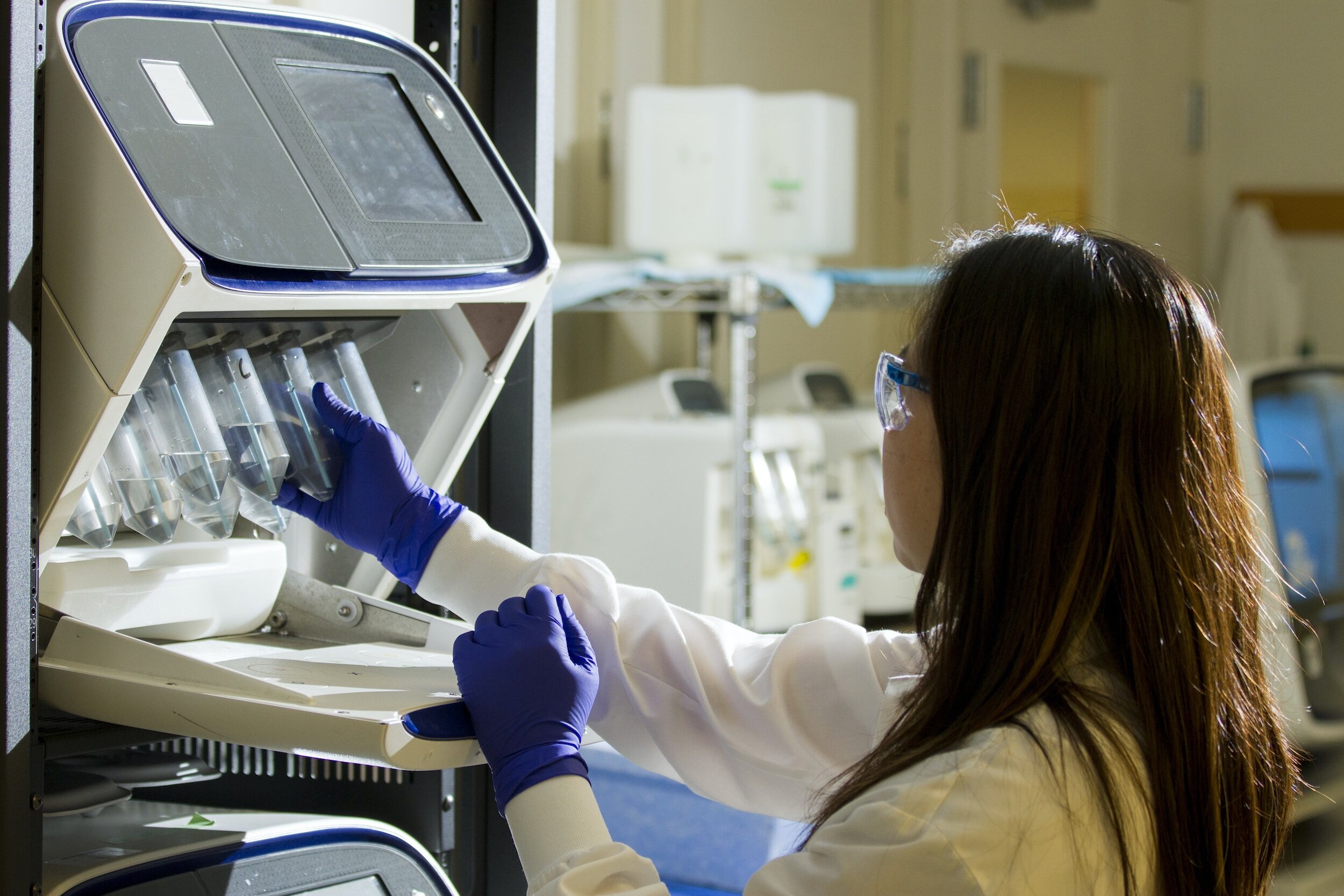
Lean management deployed for service activities
A large biotech company had a negative reputation amongst its employees and suppliers to be bureaucratic with long waiting periods in its service operations. An employee’s onboarding would take on average, over 4 months. Contractors and employees had to wait several months before being given a laptop and smart phone in order to access the necessary business applications to carry out their work. Employees would become extremely frustrated and motivation was at a low after a few weeks in their new role. Suppliers were often paid late and consequently several critical suppliers experienced cashflow issues triggered by these inefficient processes.
The company had made several large acquisitions over the years without integrating these smaller entities, therefore many processes and systems were duplicated with no end-to-end processes. Fabrice designed and led LEAN Transformation which focused on all support functions and involved some main service suppliers. He hired, trained and coached a core team of LEAN leaders and teams in each support department. The ambition was to streamline, consolidate and improve service processes to ensure a seamless execution as well as reducing Leadtime and improving employees’ experience and retention. The budget process, accounts payable, management of tangible and intangible assets, hire to retire, Legal prosecution and litigations, market access are examples of critical areas where improvements were driven across departments. The main success factors were the ability to dedicate a team of Lean experts to the main issues as well as the drive and commitment of senior executives who sponsored the Operational Excellence journey. Benefits were measured in terms of Leadtime reduction with an average of 55% reduction for most service processes. 400 Lean workshops were carried out over a period of 24 months. Thanks to the Operational Excellence infrastructure Fabrice set up, the employees felt empowered to drive the changes successfully and addressed the issues which used to make the company an unpleasant place to work and an unreliable customer for its suppliers.
The OPEX standard principles and techniques to improve manufacturing operations also work very well for Service processes where waste is often well hidden.